We use cookies on this site to enhance your experience. By continuing to browse, you agree to our use of cookies. See our Cookie Policy for more information.
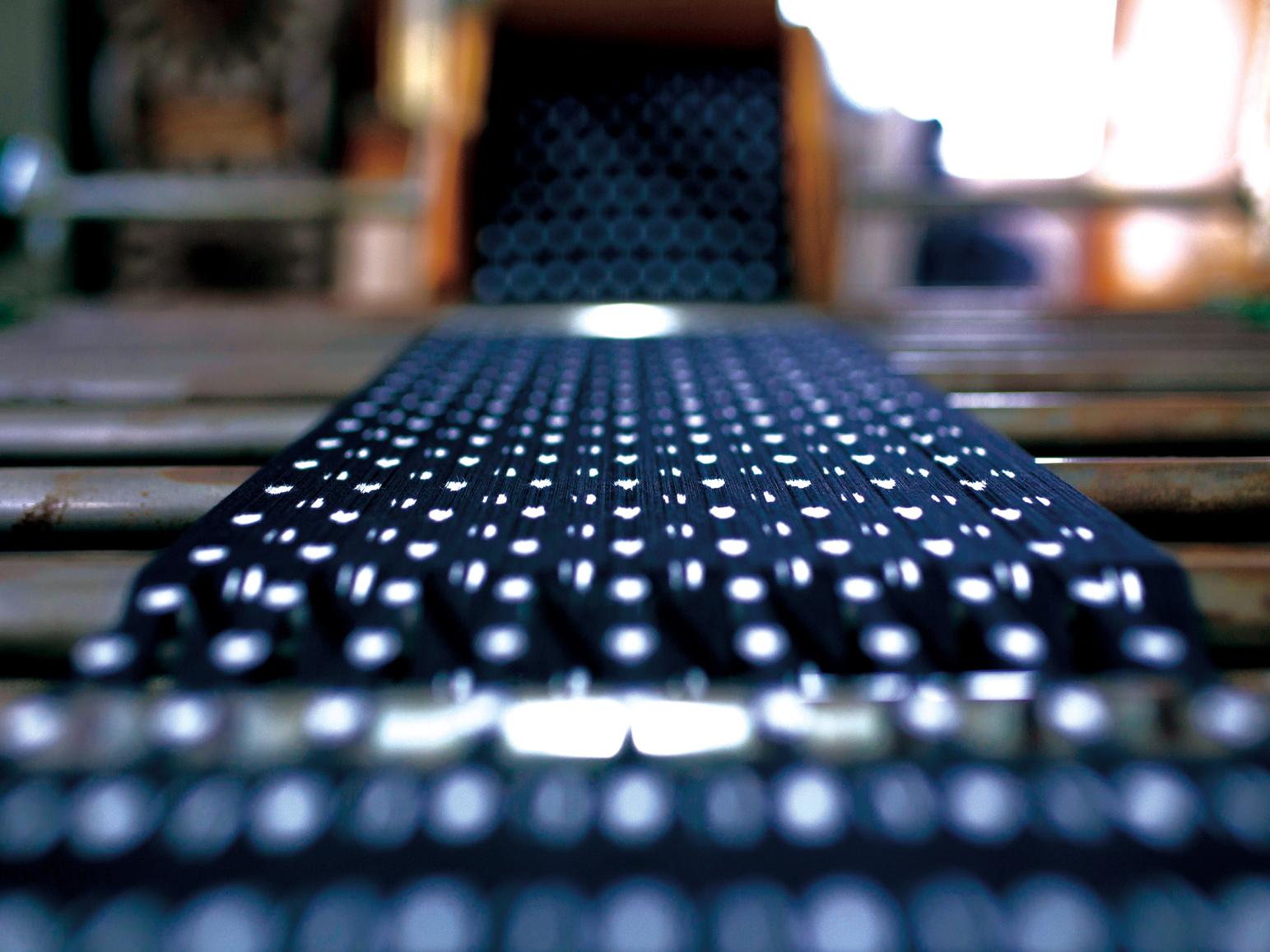
Kurume Kasuri
Warmth created by the textured pattern for rustic beauty in everyday clothes
Cotton fabric and Kurume Kasuri cloth from the Chikugo region. In the past, durable cotton fabric ideal for work clothes was hand-woven in each household. For everyday wear, plain clothes with an emphasis on practicality were common 200 years ago. The technique of bringing a gentle pattern of texture out in the fabric was created by the accidental discovery of a farmer's daughter. By dying the cotton threads then weaving, subtle misalignment occurred, resulting in a unique pattern. This is the main charm and feature of Kurume Kasuri. Now, there are not only traditional geometric patterns and indigo dye, but many products are also being made with modern patterns and pop colors.
Even though times have changed, the artisan's technology is the same. Cotton fabric that adapts to life.
Kurume Kasuri has good quality unique to cotton cloth. In the summer, it is cool and in the winter it is warm, a very important point when wearing it on a daily basis. One of the reasons its functionality is being reevaluated is that it is so comfortable. The process is very elaborate- thread is bound in bundles and dyed to produce the pattern, the dyed bundle is unwound thread by thread and woven to create one piece of cloth. It takes about 3 months to complete. In all, there are about 30 processes, making it a very labor intensive craft. While the evolution of machinery has reduced some of the burden of labor, there is no process that does not require human handcraft. It is very difficult to match the patterns of warp and weft in machine weaving, and high level artisan skill is necessary. Originally it was popular for kimono, but recently the casual items of modern life are becoming common.
The regular symmetrical patterns that emerge from Kurume Kasuri are especially good. Originally they were expressed in indigo and white but these days many colors are used.
The design is decided and the distribution of threads is calculated for the warp and weft threads to produce the pattern. The picture on the right shows the process of drawing on the threads for hand-weaving. In this, the stretch of the threads must also be considered so it is a very difficult task.
In the past, the main use for Kurume Kasuri was kimono. It is cotton fabric so its attraction is that it can be worn on a daily basis regardless of the season.
The cotton thread is dried after undergoing the bundling and dying processes. They are pulled tight while drying to reduce the elasticity of the threads. The parts of the bundle which look white are not dyed and by unwinding each thread from the bundle and weaving, the unique kasuri pattern is created.
Traditional Kurume Kasuri is threads dyed with indigo. So much effort is put in to taking care of it that the craftspeople say "the indigo is alive."
After the dying and drying are finished, the threads are separated one by one and woven. Up to this point, the process is almost the same for hand and machine weaving.
Now machines have been developed but some workshops still stick to hand weaving. The charm of hand weaving is that it can produce delicate patterns that cannot be expressed with machine weaving. Pulling apart the upper and lower warp and the weft thread is passed between that space and driven through to complete one piece of cotton cloth. It is broadly divided into "hon-gasuri," in which the pattern is made with both the warp and weft threads, “e-gasuri,” in which the pattern is made with the warp threads, and “ita-gasuri,” in which the pattern is made with the weft threads.
Hakata Gion Yamakasa festival is also registered as a UNESCO intangible cultural heritage. Actually, this festival and Kurume Kasuri have a deep connection. The outfit worn during the Yamakasa, a long happi coat, is made of Kurume Kasuri and during the festival, you can see men wearing this long happi coat all over town in Hakata.
Many products suitable for modern life made with the charm of Kurume Kasuri.
Sneakers made in collaboration with a shoe maker. White, navy, and different colored threads are woven together to create a faint texture.
Contents
01 Hakataori
02 Hakata Ningyo
03 Aganoyaki
04 Koishiwarayaki
05 Kurume Kasuri
06 Yame Chochin
07 Yame Fukushima Butsudan